Carestream Sign In
Welcome to Carestream.com's communities.
Our customers and partners have access to powerful online communities and tools. Use this overview to discover the best destination for you. Registration and sign-in are required to access these websites.
Vue Cloud Community
Carestream's Vue Cloud Community is your single point of access to the tools you need to diagnose exams, review a patient portfolio or view real-time department performance.
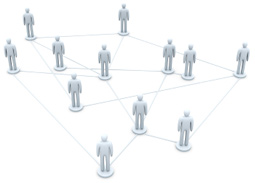
Carestream.com Communities and Tools
Welcome to Carestream.com's communities.
Our customers and partners have access to powerful online communities and tools. Use this overview to discover the best destination for you. Registration and sign-in are required to access these websites.
Vue Cloud Community
Carestream's Vue Cloud Community is your single point of access to the tools you need to diagnose exams, review a patient portfolio or view real-time department performance.
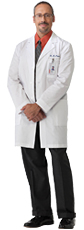
Superior Resolution Capabilities of the Industrex HPX-1 Impresses Industry Experts.
Moog Inc. is one of today’s leading worldwide designers and manufacturers of precision motion control products and systems. Founded in 1951, the company develops high-performance systems that control military and commercial aircraft, satellites and space vehicles, launch vehicles, missiles, industrial machinery, wind energy, marine applications, and medical equipment.
The Materials and Processing Engineering Department conducts approximately 1000 inspections a year on aerospace equipment for prime contractors such as Boeing and Lockheed Martin. Moog’s inspection team has recently incorporated the Industrex HPX-1 computed radiography (CR) system into its inspection lab.
“Our team was extremely impressed with the new system”, says Mascorella. “In our inspection lab we often test tube welds the size of a pencil and other small components that we call feedback wires that are almost like needles, which can often be a challenging x-ray inspection. We have to shoot each component to our ASTM E1742 aerospace industry standard. In each instance we were raising our eyebrows in wonderment, as our team was able to resolve images using the HPX-1 that you couldn’t see before without the use of film. We simply couldn’t resolve a small defect in previous CR systems like we can now with the new HPX-1 System.”
Most of Moog’s industrial inspection work requires a resolution rate equivalent to 25 micron pixel size. This high resolution is easily achieved with the HPX-1 unlike some other commonly used CR systems available on the market today.
“The Industrex HPX-1 system is the most impressive CR system we’ve seen in the marketplace to date.” According to Mascorella,“We are required to use the pentrameters that are 2T or 1T resolution,” adds Mascorella. “That is never a challenge. The real challenge is the defects themselves that are in the welds that are sometimes as small as 0.003” in diameter. Film could easily pick it up, and now the HPX-1 system can as well. We can now resolve those defects in a practical context in digital high-resolution mode.”
Film versus Digital?
“Our experience working with the HPX-1 proved that the overall exposure processing time was at least 30% – 40% faster than traditional film exposure”
Although film has had quite a foothold within the radiography industry, the new HPX-1 digital CR system is starting to make some significant strides.
“We use standard film for most of our inspections, primarily because of its great resolution, but with all of the advancements we’re now seeing with digital technology, especially in the HPX-1 system, we are getting closer to making the switch,” adds Mascorella.
Digital Also Means an Environmental Bonus for Moog
Unlike standard film-based systems, the HPX-1 digital CR system doesn’t require any chemical film processing.
“For our current film-based system we are extremely mindful of the silver we have to dispose of,” says Mascorella. “Our facility is located in a rural area and we’re on a septic system so we have to take extra precautions. We have literally had to develop a system that captures all of the fluids coming out of our film developer and treat those fluids as hazardous waste. We have a full recovery system that we sample regularly to ensure that we are doing everything by the book.
Faster Processing Speed
“Our experience working with the HPX-1 proved that the overall exposure processing time was at least 30% – 40% faster than traditional film exposure,” adds Mascorella. “It takes about 9 minutes to process a film and we can do that substantially faster with the HPX-1 system. We clocked it in the lab and the CR’s exposure rate was about thirty seconds to a minute. The loading is definitely faster and the scanning is much faster as well. It will add up at the end of the year to save us significant time and labor.”
Flexible Plates for Hard To Reach Areas
According to Mascorella most of Moog’s inspections require flexible plates.
“We have to be able to bend the plates and kink them so they have to be flexible,” says Mascorella. “With the HPX-1 system we were able to find the right plate size we needed to complete our inspections. We have some instances where the clearance might be only a ¼ of an inch and the width could be pretty slim, maybe just an inch or ½ inch. Not all of them are that tight, but some of them are. We could easily see that we wouldn’t have any problem using the plates provided with the new HPX-1 system.”
Intuitive Software Platform
“We found the HPX-1’s software easy to use and we were driving it ourselves fairly quickly,” exclaims Mascorella. “The interface itself was easy to navigate. Loading and unloading the plates and the erasing part was straightforward. We were able to use a lab technician who has very little computer experience and he was able to create exposures within a ½ hour.”
A Front-runner in Today’s Competitive Marketplace
“We’ve had the opportunity to demo a couple of CR systems from Fuji, GE and VMI, but by far The Industrex HPX-1 system is superior, especially as it relates to resolution,” says Mascorella. “The system’s ability to capture the small detail was the real eye opener for us. The speed of the exposures and all of the digital benefits regarding manipulation aspects were great, but it really was the resolution we were hunting for when we consider a CR system.”
A Recommended Computed Radiology Solution
“Most of the people we work with are all in the same boat. We weren’t very happy with the CR systems we were experiencing in the marketplace to date, and now that has all changed with the Industrex HPX-1 system. So what I’ve been saying to our prime contractors and others within the industry is, ‘Take a look at this particular system.’ I think we’re there as far as resolution goes. It’s really come a long way.”
HPX-1 Product Benefits
Powerful
• Industry leading viewing and analysis software
• Better than 50 resolution and 10 lp/mm
• True 25 x 25 pixel pitch
• High speed for improved productivity
Flexible
• Accepts flexible plates and rigid cassettes
• Handles the widest range of plate sizes in the industry
• Reads multiple plates at one time
• Multiple laser intensities while maintaining spot integrity
• Adjustable PMT sensitivity
Reliable
• Only system built specifically for NDT applications
• Positive internal air pressure keeps contaminants out of critical areas
• Vibration damping feet
Portable
• Ergonomically designed lifting handles
• Rugged travel cases
• Can be used inside or on top of travel case
About Carestream Health NDT Solutions
Carestream Health’s NDT Solutions Group designs and produces unique film and digital imaging solutions for industrial radiography. As a leading provider of computed radiography (CR) equipment, the NDT Solutions Group offers powerful in-house and portable CR systems. Other INDUSTREX products by Carestream Health include flexible phosphor plates, film digitizing systems, and a variety of films, chemicals, and processing equipment. Dedicated to high standards in quality and service, INDUSTREX systems are supported by a worldwide force of service and support professionals. To locate a distributor or for more information on these products, visit ndt.carestreamhealth.com
Choose a Region
- Africa
- Asia Pacific
- GCC-TEST
- Europe
- Middle East
- North America
- South America
Africa
Asia Pacific
GCC-TEST
Europe
Serbia
Slovakia Slovenia Spain Sweden Switzerland Ukraine United Kingdom |
Middle East
North America
South America
São Vicente and Granadina
Suriname Trinidad and Tobago Turk and Caicos Islands Uruguay U.S. Virgin Islands Venezuela Virgin Islands (British) |