Quality assurance is the overarching principle for Carestream Contract Manufacturing’s precision coating projects. We combine comprehensive analytical capabilities and expertise to improve processes, solve problems, investigate customer interests and develop coated products featuring exceptional quality and uniformity.
Our Analytical Laboratories, located in Carestream’s Oregon, Colorado and Minnesota facilities, provide the backbone for this complete diagnostic approach. Carestream’s laboratory scientists focus on three main areas to ensure impeccable quality of finished materials: raw materials’ incoming quality control (RM IQC), materials characterization, and quality assurance. All three of these functions are interconnected and performed throughout the product development process.
Incoming raw materials (such as chemicals) are evaluated to ensure they meet quality specifications. Materials characterization is a scientific process in which both raw and finished materials’ structure and properties are measured. Laboratory analysis defines a material’s solution and coating qualities, variability issues, contamination and other characteristics that might affect processing or end results. For example, inductively coupled plasma optical emission spectrometry (ICP-OES) is used to test for metal contaminants in powders; titration testing evaluates reactivity of cross linkers.
Some raw materials can only be qualified through an active evaluation of “fitness for use.” In these cases the materials are tested to make sure they are usable and will serve their intended purpose. Test method development is an important part of Carestream’s specialized expertise; our chemists design unique methods to enable analytical quantification of key quality requirements for a variety of custom products.
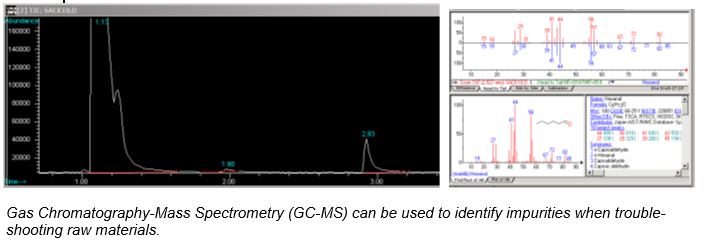
Our analytical methods continually elevate standards for new products and processes, helping improve precision and accuracy. Carestream sometimes partners with vendors on process improvement and product performance. Customer issues are carefully deliberated and addressed to consistently meet or exceed expectations.
Quality assurance achieved through rigorous testing is a cornerstone of both development and production. Carestream’s Analytical Lab is fully stocked with specialized equipment to accurately measure the full range of specifications and quality standards.
Techniques used during testing include several types of advanced microscopy, spectroscopy, chromatography, and other analysis methods. During processing, we monitor equipment performance and evaluate mixing, coating and finishing operations. While coating formulations can be precisely regulated and applied on a high-speed roll-to-roll coating web, online inspection techniques allow the coating process to run continuously while monitoring for non-uniformities that could negatively affect product performance. Online inspection and defect mapping can also enable automated culling and discarding of substandard material.
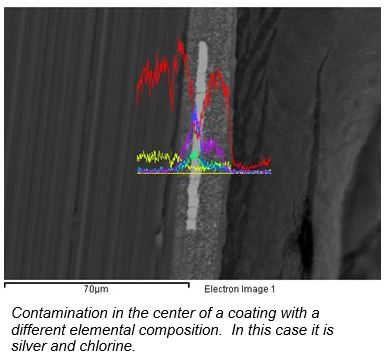
To analyze and troubleshoot point defects, samples are placed under a compound microscope for optical inspection of imperfections ranging from a few microns to several hundred microns. For larger defects, or those with significant depth, a stereoscope is used. A Fourier transform infrared (FTIR) spectrometer, which records the interaction of infrared radiation with the sample material, may also be used to determine if the composition of a defect is an organic compound such as cotton, polyester, polyvinyl alcohol, rubber, acrylate, polyethylene, etc. A scanning electron microscope (SEM), which uses electrons rather than light to form an image, can determine if a defect consists of inorganic materials like stainless steel, copper, or zinc. It can also decipher the distribution of the elements near the surface of the coating which can be used to determine the uniformity of a multi component inorganic coating. Once any defects are characterized, adjustments are made to eliminate them.
Optical image analysis techniques can be adapted in Carestream’s lab to analyze product images for particle size, number of particles, circularity, and other values. Additional quality testing metrics include film thickness, uniformity, optical clarity, haze, surface properties, adhesion, dimensional stability, reflectivity or opacity, viscosity, percent solids, thermomechanical properties, and crystallinity – to name just a few. Each factor plays a critical role in meeting specified characteristics and performance stipulations on a product by product basis.
Carestream’s comprehensive suite of testing equipment enables us to evaluate an immense range of material properties with precision. For example, we use interferometers, X-ray fluorescence (XRF), micrometers, gravimetric analysis and cross-sections to measure coating thickness. Optical properties are analyzed with HazeGard for haze, transmission and clarity. We use a cross-hatch test for adhesion. Thermal analysis techniques performed in-house include thermogravimetric analysis (TGA), dynamic mechanical analysis (DMA) and differential scanning calorimetry (DSC). Click on the links below to see a detailed list of the testing methods and instruments utilized by our engineers to characterize materials:
- Microscopy techniques
- Spectroscopy
- Elemental Analysis
- Titrations
- Particle Sizing
- Material properties
Carestream’s strategic investment in fully equipped, expertly staffed analytical laboratories supports our ability to provide reliable precision contract coating and development services. This comprehensive, start-to-finish technical assessment is a critical asset that helps ensure extremely high quality, precision-engineered advanced materials for our customers.
Carestream Contract Manufacturing’s Analytical Laboratory is equipped to perform quantitative image analysis, measuring even the most complex material characteristics.
(sample)